Custom Silicone Products Services
We can provide customized services for 3D printing and silicone products. Product development consists of concepts, 3D drawings, quick prototypes, 3D printing, and custom silicone molds.
We can design and develop various accessories and mold processing on behalf of customers. We also can produce
custom silicone parts, custom silicone products, and sponge EVA die-cutting accessories with various properties like flame retardant, shockproof, wear resistance, oil resistance, aging resistance, acid and alkali resistance, tensile resistance, tear resistance, high and low temperature resistance, chemical resistance, etc. The products are widely used in electronics, electrical appliances, communication equipment, computers, toys, lighting, sanitary ware, music equipment, sports health equipment and machinery manufacturing, and other industries.
If you are looking for reliable high quality or food grade silicone suppliers, we are your best choice.
How are silicone products made? The following is an introduction to the six processes.
1. Molding
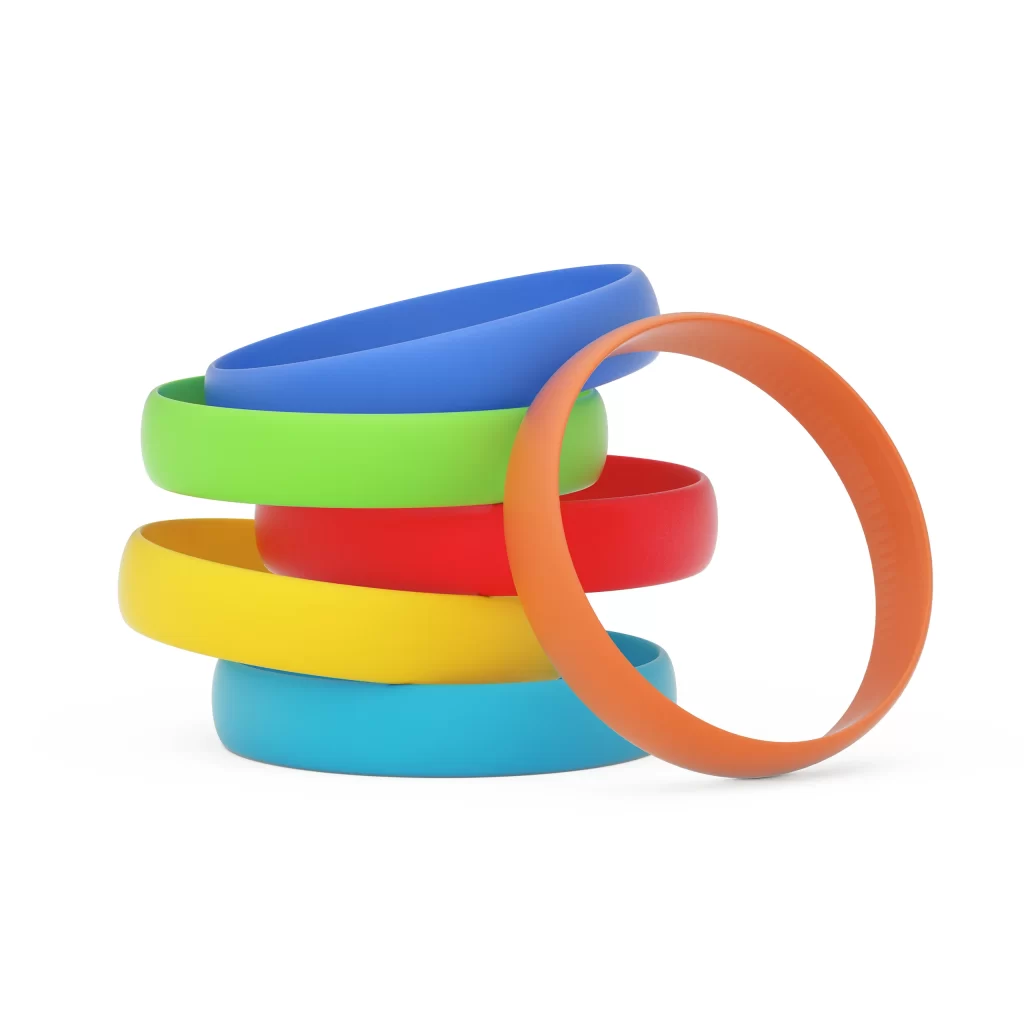
Silicone compression molding is the most common silicone manufacturing process. It mainly depends on the coordination of the mold, and the shape of the mold determines the shape of silicone products. The raw materials are usually matched with color paste, and the color is adjusted according to the universal color card number. Molded silicone products are usually made by adding curing agent silicone raw materials and applying pressure and high-temperature sulfur to solid-state molding through a vulcanizer. The semi-finished products are obtained. The hardness of molded silicone products is usually 30°C-70°C. The process is relatively simple and applicable to all silicone products. In modern society, molded products are widely used in the silicone industry. They are used to make industrial accessories, custom silicone buttons, gifts, customized silicone bracelets, watches, mobile phone covers, tableware, cushions, etc.
2. Injection
Liquid injection molding is the production of finished silicone products by China injection mould and injecting silicone. It is a high-quality requirement and combines liquid silicone and plastic. Generally speaking, this kind of product is relatively soft. For example, it is used to make human simulated organs and medical chest pads, as well as some silicone products with delicate structures that are difficult to be made by molding.
Its products have good thermal stability, cold resistance, excellent electrical insulation properties, and will not produce toxic substances when burned.
Therefore, it has become an irreplaceable material in producing and designing medical supplies, automobiles, baby products, medical supplies, diving supplies, kitchen utensils, and seals.
3. Extrusion
Extrusion molding, using a silicone extrusion machine, extrudes silicone into a plate shape, tube shape, or long regular shape silicone products. The extrusion moulding process is relatively simple, and most of them are strips. Generally, the shape of extruded silicone is long so that it can be cut at will. It is commonly used in the field of medical and mechanical equipment and can also be used as a buffer in packaging.
4.Calendering molding
The silicone rubber is kneaded, mixed with silica, silicone oil, etc., to make a mixed rubber, and then rolled out with a calender.
The longitudinal and transverse physical and mechanical properties of the films prepared by the calendering method are significantly different, which is the calendering effect. Specifically, the longitudinal tensile strength of the film is greater than that of the transverse. The transverse elongation at the break of the film is greater than that of the longitudinal. And the longitudinal shrinkage of the film is greater than that of the transverse.
The calendering effect is the result of the orientation of macromolecules, needle-like and flake-like compounds along the calendering direction during the calendering process. The calendering effect is related to the composition of the compound, calendering temperature, speed ratio, and other factors.
It is used for larger products, such as silicon wafer, transparent silicone rubber sheet, etc.
5. Perfusion
The operation method of filler molding or pouring silicone mold: filling mold or pouring mold is used for relatively smooth or simple products. There is no mold line, saving manpower and time. The product or model you want to reproduce is surrounded by rubber or glass plates, which are passed through a vacuum pump, and the outgoing silica gel is poured directly into the product. After the silica gel is dried and formed, the product is taken out, and the mold is formed. The perfusion mold is generally made of silica gel with relatively soft hardness so that it is easier to demould and will not damage the product in the silicone mold. It belongs to the combination of solid and liquid and is used for mobile phone cover, luggage protective cover and other products.
6. Coating
Silicone coating process has multiple characteristics with fast vulcanization, strong adhesion, good fluidity, and easy defoaming. The catalyst of the platinum complex is non-toxic and tasteless. It has good air permeability, heat resistance, and certain tensile strength after molding (use temperature -60℃~200℃).
Excellent non-slip performance, no pollution, low hardness, bonding firmly. High tear, high transparency, good tensile properties. Wear resistance, washing resistance, high-temperature resistance, high three-dimensional level, smooth, soft, good elasticity. Resistant to water washing and dry cleaning.Suitable for fabrics with anti-aging effects, such as silicone gloves, silicone rain boots, etc.
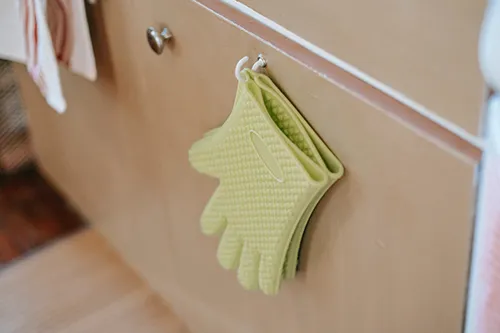
FAQ:
- What color can silicon be made?
The raw material of silica gel, originally a transparent color with colorless and odorless, is a kind of high-living material that can use color master to add various colors. The color masterbatch of silica gel can reach thousands of colors. Still, it needs to be carefully adjusted to achieve good results, which is also an essential technology for silicone manufacturers. - Is silicone smell harmful?
Silicon is environmentally friendly and non-toxic. It does not react with any substance. Except for strong alkali and acid
alkali, it can be used in any environment for a long time. - Why is silicone not resistant to acid and alkali and not resistant to aging?
What temperature can silicone withstand? The answer is about 200 degrees! Why can silicon withstand high temperature but not resist high corrosion products? Silicone oil is one of the main reasons. Silicone oil can be mixed with vulcanization to make catalysts with different components to reduce its viscosity, and it can also be adjusted with alkaline substances to increase the viscosity. In the process of making silicone, it is recommended that customers do not add any silicone oil. The necessary dosage should be at most 5% to 10% because too much silicone oil will destroy the molecular weight of silica gel. And the produced silica gel will not be resistant to acid, alkali, and aging, so adding as little silicone oil as possible to the raw material of silica gel can avoid conflicts with highly corrosive chemicals. - Why do silicone products appear yellow?
The phenomenon of yellowing is the nature of ordinary silicone products. Generally, the products will appear yellowing after being used for too long after environmental changes. However, the addition of an anti-yellowing agent can achieve the phenomenon of no yellowing or the use of food-grade silica gel raw materials and gas phase silicone raw materials. High transparency, high-strength, high-quality silicone in itself will not turn yellow. So the product you buy belongs to ordinary silicone, and no anti-yellowing agent is added to cause the product to turn yellow.