custom ceramic parts and components
What is Ceramic CNC machining?
Ceramic CNC machining refers to the process of using computer numerical control (CNC) machines to shape and fabricate ceramic materials into custom precision parts and components. It involves the precise control of CNC machines, which are computer-controlled tools that can perform various machining operations such as cutting, milling, drilling, and grinding.
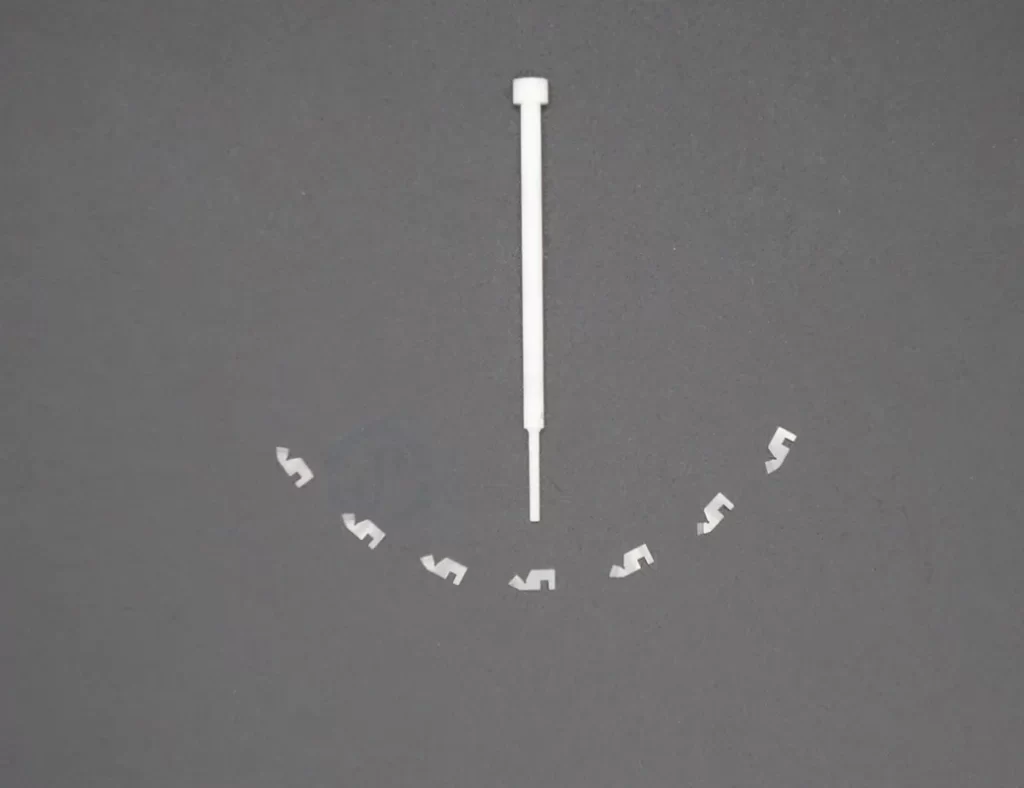
What are the advantages of Ceramic CNC machining?
Precision and Accuracy:
The high precision and accuracy of CNC machine tools enable tight tolerances and complex geometry in custom ceramic parts.
Efficiency and Productivity:
CNC machining is an efficient, automatable process that allows for faster production times and increased productivity.
Versatility:
CNC machines can work with various ceramic materials, allowing for a wide range of applications in different industries.
Consistency and Reproducibility:
CNC machining ensures consistency and repeatability of results, suitable for prototyping and mass production.
Ceramic CNC machining finds applications in industries such as aerospace, electronics, medical, and industrial manufacturing, where ceramic parts are required for their unique properties, including high temperature resistance, hardness, wear resistance, chemical resistance, and electrical insulation.
What are the common Machinable Ceramic Materials?
Machinable ceramic is available in a variety of materials, each with its own unique properties and applications. Some commonly machinable ceramic materials include:
Material | Capacities | Applications |
Alumina (Aluminum Oxide) | Alumina is a versatile ceramic material known for its high mechanical strength, electrical insulation, and resistance to wear and corrosion. | It finds applications in electronics, aerospace, automotive, and medical industries. |
Zirconia (Zirconium Oxide) | Zirconia offers exceptional mechanical properties, including high strength, toughness, and resistance to wear. |
It is commonly used in applications that require high reliability and durability, such as bearings, cutting tools, and medical implants. |
Silicon Nitride | Silicon nitride ceramics exhibit excellent thermal shock resistance, high strength, and low thermal conductivity. | They are widely used in applications such as cutting tools, engine components, and ball bearings. |
What are the main application industries for ceramic parts and ceramic components?
The versatility and unique properties of machined ceramics make them suitable for a wide range of industries, including:
Industries | Industries | Applications |
Aerospace | Machined ceramics find applications in aerospace industry due to their high temperature resistance, durability, and low weight. | Ceramics components such as parts for engines and radar components. |
Electronics and Semiconductor | Ceramics are used in electronics and semiconductor manufacturing that require excellent electrical insulation and thermal management. | Applications such as insulators, circuit boards, and specialized components. |
Medical and Dental | Machined ceramics are utilized in medical and dental due to their biocompatibility, wear resistance, and resistance to chemical corrosion. | Applications for components such as implants, prosthetics, surgical tools, and dental restoration materials. |
Industrial Manufacturing | Ceramics are widely employed in industrial manufacturing due to their hardness, wear resistance, and high temperature stability. | For applications such as cutting tools, wear-resistant components, machinery parts, and specialized equipment. |
Conclusion
Machined ceramics offer a wide range of advantages, making them highly sought-after for the production of custom ceramic parts and ceramic components. It you are in need of high-quality custom CNC ceramics parts, our ceramic machining service can meet your specific needs with precision and reliability. To learn more about us, please visit our website:or send your requirement to us (E-mail:info@uneedpm.com).