Custom PVD Coating Service – TiN PVD Coating
What is TiN PVD Coating?
TiN coating, short for Titanium Nitride coating, is a hard, wear-resistant, thin film coating that exhibits excellent adhesion to various substrates. TiN coating process is one of the most well-known PVD coating process (short for Physical Vapor Deposition) , resulting in a uniform and dense layer of TiN on the substrate surface. TiN PVD coating provides enhanced surface properties, including hardness, durability, and aesthetically pleasing appearances.
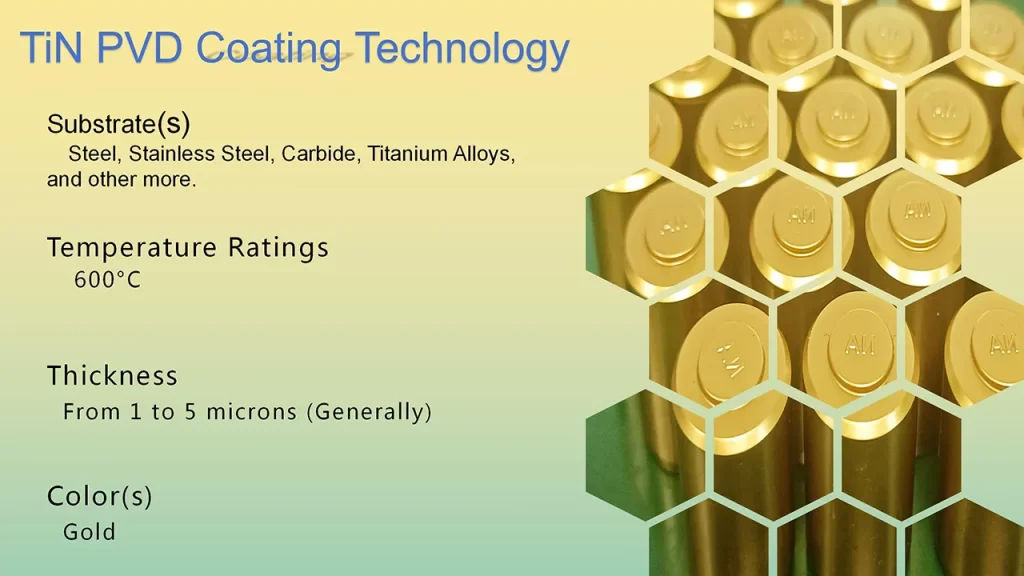
What is the Process of TiN PVD Coating?
1.Cleaning:
The substrate is thoroughly cleaned to ensure proper adhesion of the coating.
2.PVD Deposition:
The substrate is placed in a vacuum chamber with the titanium target.
Ion bombardment and reactive gas are used to vaporize the titanium atoms, which then react with nitrogen gas to form TiN.
The TiN vapor deposits onto the substrate, forming a thin film coating.
3.Cooling:
After deposition, the coated substrate is cooled to ensure a smooth and uniform surface.
What are the Advantages of TiN PVD coating?
Titanium Nitride (TiN) PVD coating offers numerous benefits across various industries. Here are some of the key purposes of TiN PVD coating:
Hardness and Wear Resistance:
TiN coating significantly enhances the surface hardness and wear resistance of the substrate, extending its lifespan and reducing friction.
Corrosion Resistance:
TiN provides excellent corrosion resistance, protecting the substrate from environmental factors, chemicals, and moisture.
Reduced Friction and Improved Lubricity:
The low coefficient of friction of TiN coating reduces frictional forces between the coated surface and contacting materials, which lead to enhanced performance, energy efficiency, and reduced wear.
Thermal Stability:
TiN PVD coating exhibits excellent thermal stability, allowing it to withstand high temperatures without significant degradation.
Electrical Insulation:
TiN PVD coating has electrical insulating properties, making it useful in applications where electrical conductivity needs to be controlled or isolated.
Aesthetic Appeal:
The golden-yellow color of TiN coating adds an attractive and luxurious appearance to the substrate, making it ideal for decorative and high-end applications.
What are the Applications of TiN PVD coating?
No. | Industry | Applications | characteristics |
1 | machinery | TiN PVD coating is suitable for manufacturing mechanical parts, such as bearings,gears, molds and dies, cutting tools,etc. | It can improve the hardness, wear resistance and corrosion resistance of the parts. |
2 | Aerospace | TiN PVD coating applies to manufacturing aircraft engine parts, such as turbine blades, turbine disks, etc. | It can improve the hardness, wear resistance and corrosion resistance of the parts. |
3 | Automotive | TiN PVD coating can be used to manufacture automotive engine parts, such as valves piston rings, etc. | It can improve the wear resistance and corrosion resistance of the parts. |
4 | Electronic | It is good to manufacture electronic components, such as capacitors , resistors,etc. | It can improve the wear resistance and corrosion resistance of the parts. |
5 | Medical | It can be used to manufacture medical devices, such as scalpels,implants, etc. | It can improve the biocompatibility and corrosion resistance of the devices. |
TiN PVD coating is a versatile and high-performance surface coating offering excellent hardness, wear resistance, corrosion resistance, reduced friction, improved lubricity, and aesthetic appeal. So it applies to numerous components across various industries.
Contact us (E-Mail: info@uneedpm.com) today to explore how TiN PVD coating can benefit your specific requirements and elevate the performance of your products.